Last issue I described some of the tools required to be a successful electric aircraft modeler. This issue, I would like to discuss some physical properties of flying vehicles that many modelers often confuse.
POWER
An electric motor converts the electrical energy stored in a battery into mechanical motion, in our case to turn a propeller (prop). The power that the electric motor consumes is called watts (W), sometimes defined as horsepower (hp). 746 W = 1 hp. Wattage is the product of the voltage supplied by the battery multiplied by the current (amperage, abbreviated: amp). A battery delivering 10 volts to a motor running at a current of 20 amps means the motor is absorbing 200watts or approximately 1/4hp. The amount of power that actually gets out to the prop is going to be a function of how efficient the motor is at converting the supplied power into mechanical motion. Some mass-produced motors have efficiencies as low as 40-50% (the way we use them) and some high quality brushless motors have efficiencies as high as 90%. Mechanical friction and the electrical/magnetic properties of each individual motor determine how much power is lost to heat, instead of turning the prop. This somewhat diminished power delivered to the prop is the power used to move the air through the propeller disk, creating thrust and forward speed.
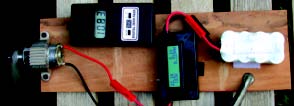
THRUST
The turning propeller accelerates the air in front of it, through the prop disk area, making it exit the rear face faster than it came in. This change in momentum of the air produces thrust, the force that overcomes the drag of the air vehicle. Thrust is often confused with power; many think that a higher thrust means more power. Often it will, but it does not necessarily happen that way. Many also think that a higher thrust means more speed! That often is exactly the opposite!
In a model aircraft as well as a full scale aircraft, thrust can be produced two ways; a small diameter prop turning very fast, or a large diameter prop turning much more slowly. With the same “input power” one can create the same amount of thrust with two completely different size props. These two propellers, however, will travel through the air at much different speeds.
Many modelers put too much emphasis on creating and measuring static thrust. Even when measured, these numbers can be deceiving. The measured thrust of a prop not moving forward (e.g., frozen in place in dead air on a bench mount) will be significantly different than the thrust measured as the prop moves through the air. Thrust diminishes with forward speed. An aircraft reaches its maximum speed when the drag of the vehicle is equal to the thrust at that speed. “Pitch speed” (often the more important term, which we will next define) makes a model move “comfortably” through the air, not thrust.
PITCH SPEED
Propellers are defined by two “physical” numbers: diameter (D) and pitch (P). If the prop is not labeled, the first dimension is easy to determine with any linear scale (egad…. ruler!) The second number requires a “pitch gage.” The pitch of a prop determines how far forward the prop would move in one revolution though a solid medium. Since we do not fly through solids, a propeller “slips” a bit. The model will always fly slower than the computed “pitch speed” based on the RPM of the prop. Without some sort of onboard instrumentation, the true speed of a model is very difficult to determine. Fortunately for us, most model prop manufacturers label their props well, and we can grossly compute how fast our model will fly if we measure the static (on the ground) RPM of the prop and use the following relationship: Airspeed (MPH) = P x RPM x .00095. A 6-inch pitch prop turning at 10,000RPM will go approximately 57MPH.
The pitch to diameter ratio (P/D) is probably the most important value for the e-modeler to understand: it affects power, thrust and speed.
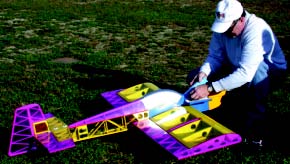
PROPELLER-MOTORAIRFRAME MATCHING
The proper matching of an electric propulsion system to any particular airframe is much more difficult than the fossil fuel internal combustion type engine. Nearly 70 years have past since the inception of the small internal combustion motor for model aircraft. Matching an engine to an airframe has had that many years of experience behind it. Though a complete explanation will take many, many pages in this magazine, I plan to offer you a little bit of the knowledge obtained on electric model flight accumulated over a much shorter time period.
It takes a specific amount of power to make any model aircraft fly well. The power delivered by the battery and electric motor must be converted to thrust, to overcome rolling friction on the ground and aerodynamic friction in the air—called drag. Power must also must be converted to speed to make sure the model flies fast enough to support the weight.
Many electric modelers use a watts/lb. (final model flying weight with batteries installed) value to first assess whether the model will fly at all. It has been generalized by many over the years, that most models need 30 W/lb. just to obtain flight. 50 W/lb. will get most models to fly “comfortably,” i.e., fast enough over the stall speed of the model not to be “dangerous.” 70 W/lb. makes for the beginnings of an aerobatic model, and 100 W/lb is reserved for racing models or the high performance climb and glide sailplanes.
PITCH AND DIAMETER
Earlier I mentioned the P/D ratio. Since we are still handicapped by having to put a fixed pitch prop on most of our models (full scale aircraft have variable pitch props or “constant speed props”), the proper P/D ratio should be chosen to match the way the model is intended to be flown. High drag models (such as WWI biplanes) appreciate P/D ratios around .5 – .6 (eg., – 12×6). These props produce exceptional thrust, but at lower forward speeds. Choose this type of prop also for “3D type” aerobatic models.
If you expect your model to fly faster (cleaner, more streamlined sport or scale models), choose props that have a P/D ratio closer to .7 – .8 (e.g., 12 x8) and use “square” props (P/D ratio=1 or greater) for high-speed models such as pylon racers (e.g., 12×12). These “square” props are typically “stalled” when the model is not moving and create a lot of noise. Once the model starts moving the prop “unstalls” and quiets down considerably.
Next issue we will discuss the different types of electric motors and speed reducers (gearboxes and belt drives) and their maximum output power. I will also illustrate a few examples of “first cut” power systems sizing using the above guidelines. This will give you the tools to understand how to select power systems for the kind of models you want to fly.
Links
Astro Flight Inc.
www.astroflight.com, (310) 821-6242
Hobby Lobby International, Inc.
www.hobby-lobby.com, (615) 373-1444
Skyborne Electronics
www.bktsi.com, (972) 267-5099